Testing Methods
Testing for this project was a simple comparison to the original design. The primary objective is to get as close to the original design as possible. With conversion casting, near net shape is the goal because almost all cast parts require post machining. An example would be the removal of the gating system. Getting as close to near net shape requires less machining which means dollars saved and manufacturing time reduced.For this project, the dimensional tolerance was set to 5% for external dimensions and 10% for internal; the internal dimension being the barrel of the adapter hub. The barrel requires intricate machining so an added 5% was to accommodate for human error and potential misalignment during solidification.
First test was the first test pour done. It was a success because the pattern cavity was full and no voids were visible. This test consisted of removing the gating system and doing a direct dimensional analysis in comparison to the original design. The dimensions needed to be within tolerance of the set requirement of 5% for external and 10% for internal. The results are as followed.
Test 1
It is shown that all primary dimensions passed the dimensional analysis exept the height of the base plate. This was caused by a failure during the assembly process. Once the base plate was assembled to the pattern bed, the curing process for the epoxy was accelerated because it was placed in an oven. The result of this process pushed the base plate up. This made an uneven connection for the base plate which had to be repaired. This resulted in a slight elevation which ultimately increased the overall height of the base plate. After this test, the match plate went through some repairs to fix this dimension.
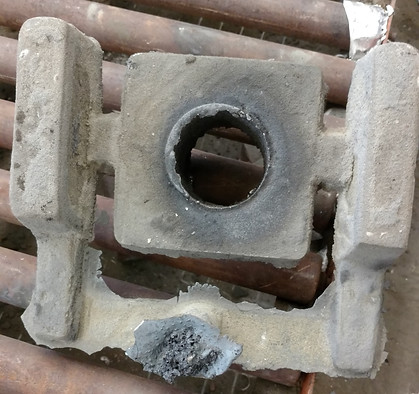

First Pour
As a result from the first pour, the cope and drag filled completely but a bit of splash is noticeable due to the liquid iron pushing the cope away from the parting line. This is fairly normal but highly unwanted. The splash is located in the gating system so it doesn’t affect the final results of the adapter hub.
Test 2
Temperature tolerance is a tricky procedure that is very hard to “standardize”. Due to the ambient temperature of the foundry, a lot of heat transfer is occurring during each pouring cycle. With a hot crucible, the temperature is checked before the pour to get an idea of how hot the metal is while it’s being poured into the flask. The temperature gets recorded and then the metal has to solidify. Because dimensions haven’t changed on the match plate, the expected results are whether or not the cavity gets filled. It has already been tested that the pattern devise works and the dimensions are within specification, this test is mainly prioritized based on when can the pattern devise be in use. After solidification, the pattern gets removed from the flask and goes through a visual inspection to check if there are voids, splash, or if the metal seized. The goal is to get the adapter hub cavity completely filled.
The overall performance of the pattern devise is quite impressive. The melting temperature of iron is around 2200F and the test was done at 2350F and 2275F. The most impressive part of this test is that the material was carbon rich. Because random pieces of scrap iron were placed into the crucible, it’s hard to gauge what alloy is really inside the crucible. After the test, crystalized carbon (not diamonds) mixed with iron slag was found inside the crucible. This is due to rich carbon that cant bond with the iron. This could have been avoided if more raw iron was placed into the mixture and melted down to create one consistent gray iron alloy.


The images above are a test pour at 2250 degrees fahrenheit
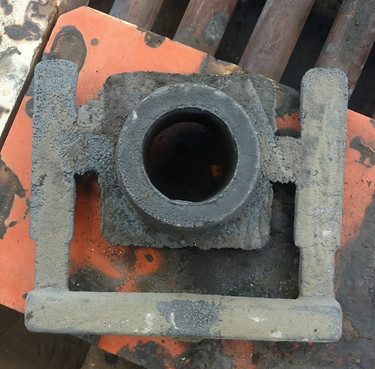
