Analysis
The design process for the adapter hub is quite simple. The adapter hub is already standardized and dimensioned to fit the Victair Mistifier so the challenge is to work around the original design. The adapter hub already has a drawing so the devise will be dimensioned to those same dimensions but larger to accommodate for shrinkage during the solidification process.
The first approach for this devise is to put the most basic necessities into a match plate.A match plate or a pattern devise consists of a pattern bed, the pattern (part being made), risers, runners, and gates. The pattern bed is what houses all the components of the match plate, pattern, runners, gates and risers. Although typically made from wood, plastic and metal is still a material option. The pattern itself will be the adapter hub. Fortunately the adapter hub has already been dimensioned by the customer so the pattern will fit those requirements but include characteristics that will make the pattern suitable for casting. This includes increased dimensions for shrinkage and a taper to create easy removal from the casting flask.
The first approach was dealing with the shrinkage of the pattern. For internal characteristics, such as the internal cylindrical housing, the diameter needed to be reduced because during solidification, it will shrink from the inside out. However, for the external dimensions, material was added because the direction of shrinkage is opposite. It will be shrinking from the outside in. To keep even consistency as well as the listed requirement, 5% was used to accommodate for shrinkage. The customer wants the adapter hub to be made from steel, which has a shrinkage value of approximately 2% so with the added 3%, human error as well as imperfections in material used and possible misalignment, or just giving extra material to be machined off to ensure a smooth finish all around. The equation used was simply Χ=l*(percentage) ; percentage either being 1.05 for addition or 0.95 for reduction. For this project, this was the only real hand calculation needed.


Photos bellow show the direction of shrinkage of the pattern.
A major cast characteristic required in any match plate is a draft angle. The draft angle makes for easy removal as well as laminate flow into the pattern cavity. When it comes to “easy removal” this is directed towards the ability for the pattern to be removed from the sand after being packed. With all patterns, while sand is being packed into the flask, there is a suction or vacuum being produced between the pattern devise and the sand because there is moisture in the sand. With continuous packing, the water in the sand creates a barrier and removes as much air from the flask as possible. In order to break the vacuum, a positive draft angle is placed on all deep components of the pattern devise. While a vertical force is being applied to remove the pattern from the cope or drag, the positive draft angle allows air to come in between the pattern and sand to break the vacuum.
While material is being poured into the pattern cavity, the flow of the material actually makes a difference during solidification. Take for example; if there is a rapid flow into the flask, the material is filling the cavity at a rapid velocity and increases the probability for air pockets within the pattern. This would occur if there is a turbulent flow and the air doesn’t have enough time to be removed from that empty space. So, the material stacks above it and begins to solidify. With a positive draft, the material flows evenly into the cavity instead of “dropping” into it.
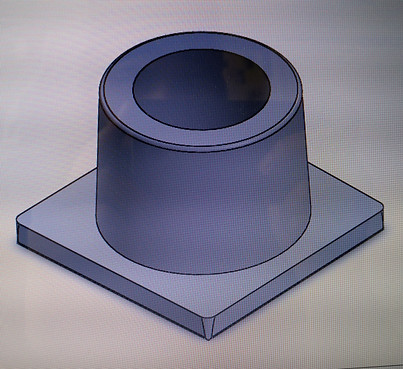
A phenomenon that occurs during each pour is a buoyant force that develops as the cavity begins to fill. As you may know, buoyant force is equal to. To counteract this force, the weight of the sand in the cope holds the flask together and prevents material pouring out of the parting line. Because a sand core is in the cavity, the sand core gets “attacked” by the buoyant force and can cause the core to shift from its intended position. For precautions, extra weight is added to the top of the flask.
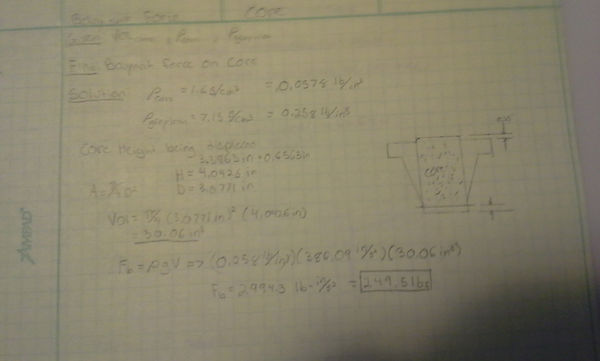
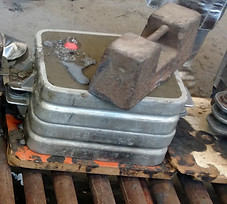