Testing Result
Testing outcomes are quite simple; did the pattern devise work, did the mould get filled all the way, and did the dimensions fit the specifications of the required 5% external and 10% internal? During the dimensional analysis, the test was quite successful. Because casting process and shrinkage is now standardized, the pattern can be designed based of off known shrinkage of the material being used. For iron it is 1-2%. Making the tolerance 5% gives extra room for error and because the foundry can only deliver class C castings, it was an adequate value. All measurements passed except for height. This is due to the damage done during construction in March. The base plate did not have a flush connection to the cope section of the pattern bed which ultimately changed the elevation of the base plate and thus increasing the height of the base plate. The inner barrel had a tolerance of 10% because sand cores are unpredictable. They can move during the pour or can break once in contact with hot metal. 10% might seem like a generous range but because there is so much detailed post machining, it was suitable to the designer and recommended by the customer.
The temperature tolerance was an unexpected huge success. Most match plates are designed for specific temperatures, specific foundries, and specific materials. The overall performance of the pattern devise is quite impressive. The melting temperature of iron is around 2200F and the test was done at 2350F and 2250F. The most impressive part of this test is that the material was carbon rich. Because random pieces of scrap iron were placed into the crucible, it’s hard to gauge what alloy is really inside the crucible. After the test, crystalized carbon (not diamonds) mixed with iron slag was found inside the crucible. This is due to rich carbon that cant bond with the iron. This could have been avoided if more raw iron was placed into the mixture and melted down to create one consistent gray iron alloy.
Fahrenheit
The pattern device works in a variety of temperatures, it fits the dimension specifications, and it worked while damaged. The device has been repaired and there is now a solid connection between the base plate and the cope pattern bed. Because of this repair, it is expected that the base plate will now be in 5% tolerance specification.


Match Plate Repair
Match plates have a tendency to get damaged while in production. Whether they are made from wood or metal, some sense of failure will occur; dimensions change, tolerances get out of spec, and components break. For this repair, the objective was to salvage as much of a damaged match plate as possible and return it to its original design while also being within specifications of the design. The cope of the match plate was damaged during construction. To save costs, the pattern had to be removed from the pattern bed, remove the epoxy that connected the base plate pattern to the pattern bed, connect the separated portions of the base plate, and then get reattached to the pattern bed. It is crucial to this repair that the overall dimensions of the pattern stay within a 5% tolerance for external and 10% for internal dimensions of the original design and there is a solid connection between the base plate and the pattern bed. If the connection isn’t level, post machining for the adapter hub becomes much harder and a change in elevation will cause problems for a concentric connection for the sand core that is placed in the middle.
The base plate of the pattern was cracked in the middle and has now created two parts. This portion of the match plate was removed and repaired. This process was done by aligning both portions of the base plate so that the pattern is squared to all sides then reattaching both portions. The crack wasn’t just a separation but a rift with an empty cavity. If the pattern is squared and glued together, the cavity can be filled using a variety of material such as wood glue, epoxy, clay, or even hot glue.

With the pattern removed from the pattern bed, the pattern bed was cleaned. This consists of removing the epoxy that made the original connection between the base plate and the pattern bed. There are multiple ways to approach this problem but the removal of this layer of epoxy was tough. This can be done by applying acetone and scrubbing the epoxy off, taking a putty knife and scraping it off, or the most tedious method, sanding it until only wood is visible.
Once the pattern bed was cleaned and the base plate was now one piece, the base plate was reconnected to the pattern bed. A quick setting epoxy was used to reassemble the base plate to the pattern bed. This was to ensure that once the weights were applied to the base plate, the pattern wouldn’t shift from its set position.
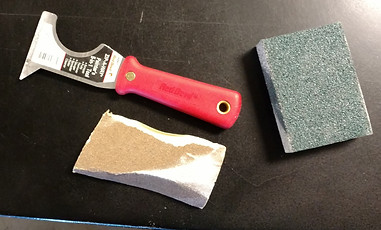


To fix the cavity, the base plate was first glued and set into position. After the epoxy set and no separation with the base plate and pattern bed was visible, the crack was filled with quick set repair putty. This was recommended by a Jim Justin who is a master patternmaker for Puget Sound Pattern Works. Because the cavity result was vertical expansion, almost little damage was done to the dimensions. The vertical expansion created the “nipple” where the core is set got slightly taller so after the putty and epoxy cured overnight, the “nipple” got sanded and the repair was complete.
Final Product
After removing the gating system and removing the excess sand that stuck to the iron, the adapter hub is ready for grinding. The grinding process was quite simple, it consists of griding any splash and burrs around the surfaces. This would allow adapter hub to be easily placed into a chuck then faced off the bottom surface and the barrel would get cleaned. Then the adapter hub would be placed into a vise and the corners would get drilled and tapped. The estimated machine time is roughly an 35 minutes depending on who writes the code and which machine is being used. It is averaged that the foundries within the Washington area can make one adapter hub for roughly 75 dollars and this includes post machining.
