The objective of this project is to replicate a predesigned component for a machine used in agriculture. The idea is to create a pattern as close to the original component as possible in order to reduce manufacturing cost and labor time. Using casting techniques, the project wraps around the method of conversion casting. This involves creating a pattern that matches the original part but adding necessary adjustments in size and components in order for the part to be cast.
Size reduction and addition is due to shrinkage depending on the material. The material for this project will be gray cast iron and has a shrinkage value of approximately 1.0%. This value varies due to the material composition such as carbon and silicon percentage by weight. With this in mind, dimensions are sized to accommodate for shrinkage.
The pattern must be able to be place into the sand and removed with minimal damage to the mould. Draft angles are added to all side sections of the adapter hub to allow easy removal.
Components necessary for a cast pattern are the gating system and risers. The gating system allows liquid metal to flow from the sprue well, through the runners, and then into the pattern cavity. The risers are an addition to the gating system that helps fill the pattern cavity. The risers are a section in the pattern that are high than the pattern itself. This system works by filling up the riser portion of the pattern and then uses gravitation force to fill any empty space in the pattern cavity. It’s a simple addition that ensures that the pattern cavity gets completely filled with material.
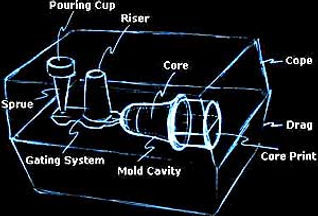
Note: Project still under construction